Four Common Defects in Injection Molding
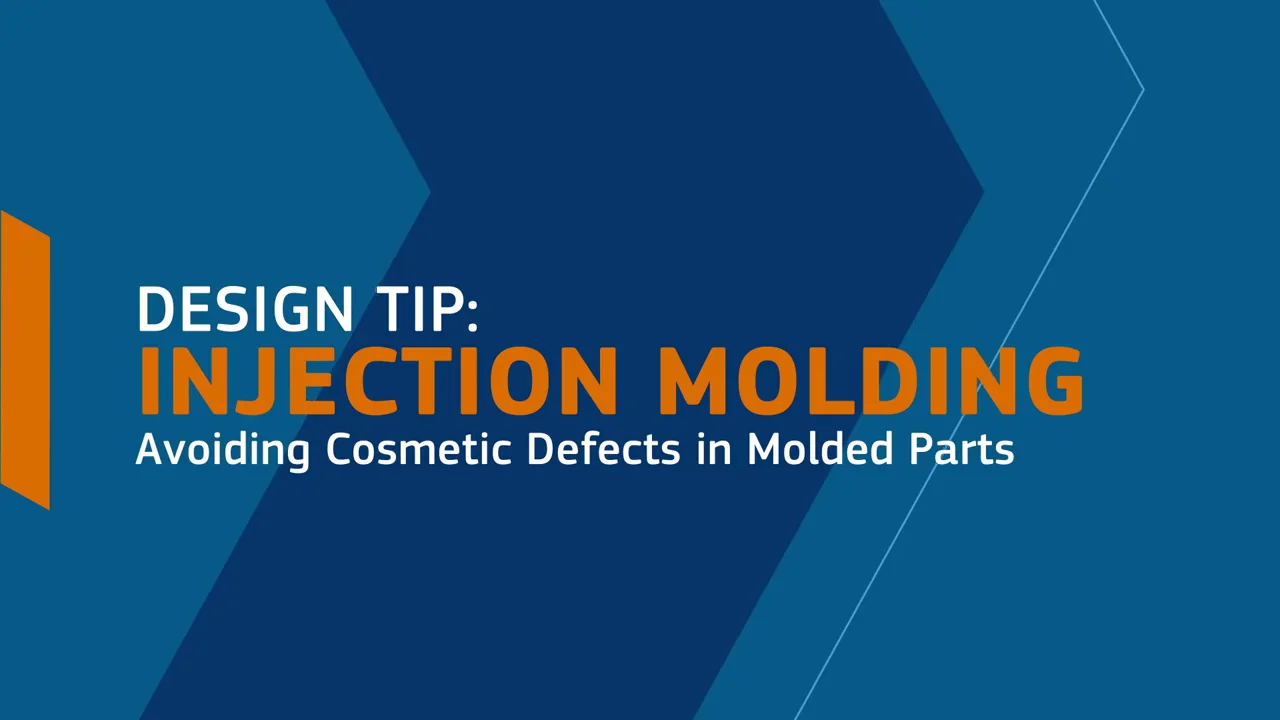
Injection molding stands as a dynamic manufacturing procedure known for crafting plastic parts and components with exceptional precision and efficiency. This intricate technique entails the injection of molten plastic into a meticulously designed mold, where it undergoes a cooling process to solidify into the desired shape. Renowned for its versatility and cost-effective nature, injection molding has become a cornerstone in various industries, delivering top-notch quality and consistency. Join us in this blog post as we delve into the realm of injection molding defects, unraveling the challenges and solutions that pave the way for enhanced production outcomes.
Weld Lines
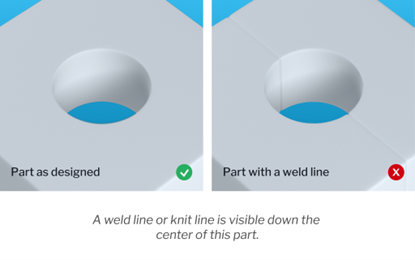
Also known as knit lines, these imperfections indicate the juncture where two streams of molten resin converge as they navigate through the mold structure. Typically occurring around areas of the geometry that feature apertures, this phenomenon arises when the plastic material flows and encircles each side of a hole, leading to the meeting point of the two flows. If the temperature of the material is not precisely regulated, the fusion of these flows may be compromised, resulting in the formation of a discernible weld line. This visual defect not only compromises the aesthetics but also diminishes the overall robustness and longevity of the component.
Short Shots
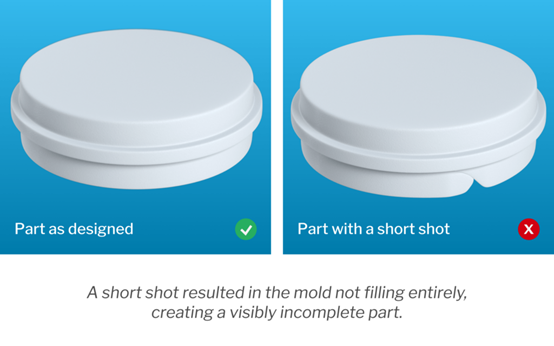
“Short shots,” a term commonly used in injection molding, describe situations where the resin fails to completely fill the mold cavity, leading to incomplete and nonfunctional parts. These occurrences can be attributed to various factors within the molding process. Typically, short shots result from constricted flow within the mold, often caused by narrow or blocked gates, trapped air pockets, or inadequate injection pressure. Material viscosity and mold temperature also play significant roles in the occurrence of short shots. To mitigate the risk of short shots, it is advisable to increase the mold temperature and integrate additional venting in the mold design to facilitate the proper escape of air. By addressing these factors proactively, manufacturers can enhance the likelihood of achieving complete and high-quality mold fillings, thereby minimizing the occurrence of short shots in injection molding processes.
Warping
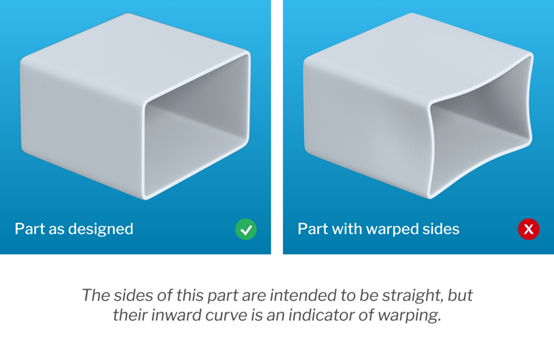
Injection molding warping is a common issue that arises from unintended twists or bends in the final product due to uneven internal shrinkage during the cooling phase. The root cause of warping defects in injection molding can often be traced back to non-uniform or inconsistent mold cooling, leading to internal stresses within the material.
Preventing warpage defects in injection molding requires careful attention to the cooling process. Ensuring that parts are allowed adequate time to cool down gradually can help prevent the formation of internal stresses that may distort the component. Maintaining a uniform wall thickness in the mold design is crucial as it promotes consistent flow of plastic through the mold cavity in a singular direction, reducing the likelihood of warping issues.
It’s important to highlight that materials with semi-crystalline structures are more prone to warping, emphasizing the significance of selecting the appropriate materials and implementing precise cooling strategies to mitigate the risk of warpage defects in injection molding processes.
Electronics Industry
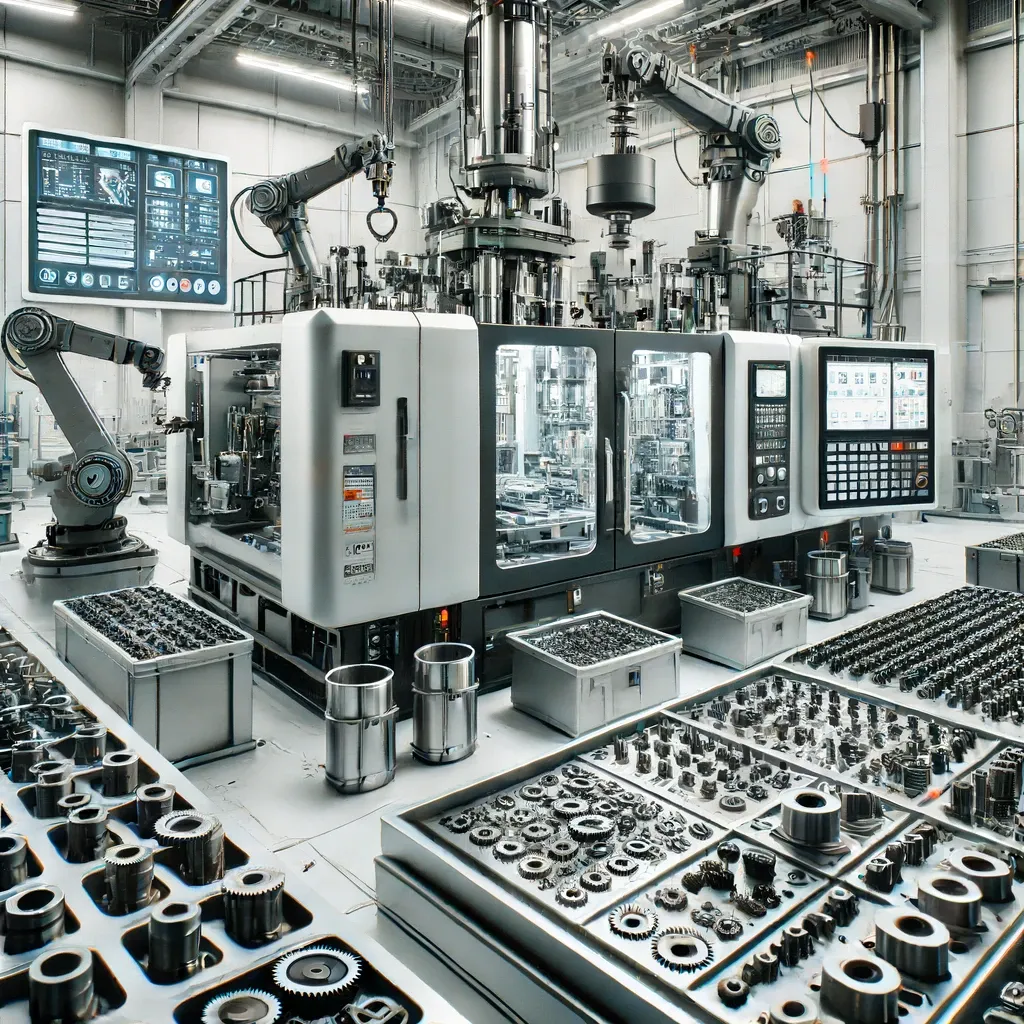
Component Housings
Injection molding is crucial in producing housings for electronic components. Items like connectors, switches, and sensors are often encased in plastic shells made through this process. The accuracy and consistency of injection molding ensure that these components fit perfectly and function reliably.
Cable Insulation
The insulation for electrical cables is often produced using injection molding. This application is essential for ensuring the safety and durability of electrical systems, preventing short circuits and other electrical issues.
Jetting
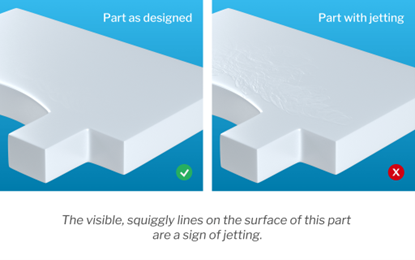
Jetting defects in injection molding can present challenges stemming from an uneven solidification process. Jetting occurs when an initial stream of resin enters the mold and begins to solidify before the cavity is entirely filled. This premature solidification gives rise to visible, meandering flow patterns on the surface of the part, compromising both its aesthetics and structural integrity.
To address jetting defects effectively, reducing the injection pressure is often recommended to facilitate a more gradual and uniform filling of the mold. Moreover, adjusting the mold and resin temperatures can aid in preventing premature solidification of the resin streams, thereby minimizing the occurrence of jetting. Strategically placing the injection gate to ensure that the material flows through the shortest axis of the mold is another practical approach to mitigating jetting issues in injection molding processes. By implementing these measures thoughtfully, manufacturers can enhance the quality and consistency of their molded parts while reducing the likelihood of jetting defects.
Conclusion
Injection molding can indeed serve as a highly efficient method for manufacturing consistent plastic parts. However, achieving top-notch end-products requires meticulous attention to detail and a proactive stance towards risk management. Every individual involved in the product development journey, starting from the design phase to the final fulfillment stage, must uphold diligence to uphold quality standards and mitigate common plastic injection molding issues.
When selecting a manufacturing partner like suntechplus, who boasts expertise in identifying and troubleshooting prevalent defects in injection molding, you pave the way for top-quality parts that are delivered punctually and within budget constraints. By collaborating with a seasoned on-demand manufacturing expert like us, you not only gain access to our proficiency in defect resolution but also benefit from our design consultation and optimization services. These additional offerings ensure that every team can create functional, refined, and high-performance parts in the most efficient manner possible. Reach out to us today to explore further details about our injection molding services and discover how we can support your manufacturing endeavors.
Import from China Guide
For beginners who don’t know what to buy & sell, have 0 experience about importing from China, you can get all questions answered in this tutorial.
(10 video courses included)